Blog
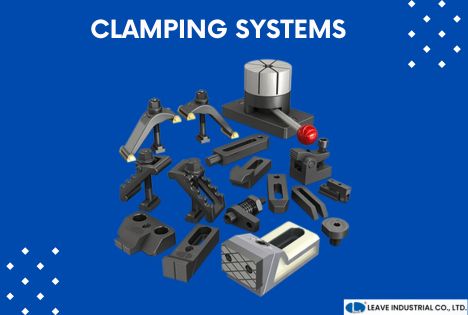
Introduction
In the sophisticated world of modern manufacturing and machining, the role of clamping systems is indispensable. These systems ensure the secure positioning of workpieces, facilitating precise operations, enhancing safety, and boosting productivity across various industries. At LEAVE, we pride ourselves on delivering state-of-the-art clamping solutions that cater to a diverse range of industrial requirements.
Types of Clamping Systems
Understanding the different types of clamping systems is crucial for selecting the right one for your needs:
- ♦ Hydraulic Clamps: Ideal for applications requiring significant clamping force. These clamps use fluid power to apply pressure, offering robustness and reliability for heavy-duty operations.
- ♦ Pneumatic Clamps: These clamps use air pressure for operation, making them suitable for quick clamping in automated production lines. They are lightweight and easy to adjust, providing speed and flexibility.
- ♦ Mechanical Clamps: Traditional and versatile, these clamps use mechanical force to secure workpieces. They range from simple manual clamps to sophisticated automated systems, suitable for detailed crafting or industrial scale manufacturing.
- ♦ Magnetic Clamps: Utilize magnetic force to hold ferromagnetic materials. They allow for rapid setup changes and are particularly useful in welding and assembly operations where quick repositioning is necessary.
Each type offers specific advantages tailored to particular operational needs, highlighting the importance of understanding the nuances of each to optimize your manufacturing processes.
Key Components and Functionality
The effectiveness of a clamping system hinges on its components, which include:
- ♦ Clamps: The actual contact points that hold the workpiece. Their design varies widely depending on the type of clamping system.
- ♦ Bases and Supports: These provide a stable foundation for the clamps and the workpiece, crucial for maintaining alignment during operations.
- ♦ Actuators: These are the driving force in automated clamps, responsible for moving the clamps into position and applying the necessary pressure. They can be hydraulic, pneumatic, or electric.
Understanding how these components work together helps in setting up systems that maximize efficiency and accuracy.
Benefits of Effective Clamping
A well-implemented clamping system offers numerous benefits:
- ♦ Enhanced Stability: Secure clamping reduces vibration and movement, crucial for high-precision machining.
- ♦ Increased Accuracy: Ensures that the workpiece remains in the correct position throughout the machining process.
- ♦ Operational Efficiency: Speeds up the setup and changeover times, significantly enhancing throughput.
- ♦ Improved Safety: Reduces the risk of workpiece slippage, which can cause damage to machinery and harm operators.
Choosing the Right Clamping System
Selecting the right clamping system is crucial for optimizing manufacturing efficiency, precision, and safety. Consider these key factors:
- ♦ Workpiece Material: Choose strong hydraulic or magnetic clamps for harder materials to provide necessary force without damage. For softer materials, opt for mechanical clamps that offer gentle handling.
- ♦ Production Volume: In high-volume production, efficiency is critical. Pneumatic clamps offer quick operation, reducing cycle times, while automated mechanical systems can handle continuous operations with minimal supervision, enhancing productivity and reducing costs.
- ♦ Specific Applications: Tailor your choice to the needs of specific tasks. CNC machining requires precise, programmable clamping systems for consistent quality. For flexible production setups, consider modular systems that allow for easy adjustments and configuration changes.
Additionally, think about:
- ♦ Environmental Factors: Ensure the clamps can withstand your operating environment, such as choosing corrosion-resistant materials for damp or corrosive conditions.
- ♦ Ergonomics and Safety: Opt for easy-to-use systems that minimize operator strain and enhance safety.
- ♦ Future Scalability: Select systems that can be scaled or upgraded easily, ensuring they grow with your production needs.
These guidelines will help you choose a clamping system that not only meets your current requirements but also adapts to future changes, providing a lasting solution for your manufacturing challenges.
Maintenance and Care
Regular maintenance of clamping systems is critical:
- ♦ Routine Inspections: Check for signs of wear and tear, especially in mechanical parts.
- ♦ Regular Cleaning: Keep clamping systems free of debris and lubricate moving parts to prevent malfunction.
- ♦ Calibration Checks: Ensure that hydraulic and pneumatic systems maintain correct pressure levels to avoid over or under clamping.
Innovations and Future Trends
The clamping systems market is evolving with trends like:
- ♦ Automation and Connectivity: The rise of Industry 4.0 technologies is integrating clamping systems into networked environments where they can operate in sync with other machinery, controlled remotely through intelligent systems.
- ♦ Material Science Developments: Innovations in materials are leading to lighter, stronger, and more durable clamps, expanding their capabilities and applications.
- ♦ Environmental Considerations: Eco-friendly designs that reduce power consumption and increase efficiency are becoming more prevalent.
Conclusion
Choosing the right clamping system can dramatically influence the quality, safety, and efficiency of manufacturing operations. At LEAVE, we are committed to providing top-tier clamping solutions tailored to meet the exact needs of our clients' varied operations.
Explore Our Solutions
Discover how LEAVE's innovative clamping systems can elevate your manufacturing capabilities. Contact our expert team for more information. We are eager to help you streamline your operations and achieve new levels of manufacturing excellence.