Blog
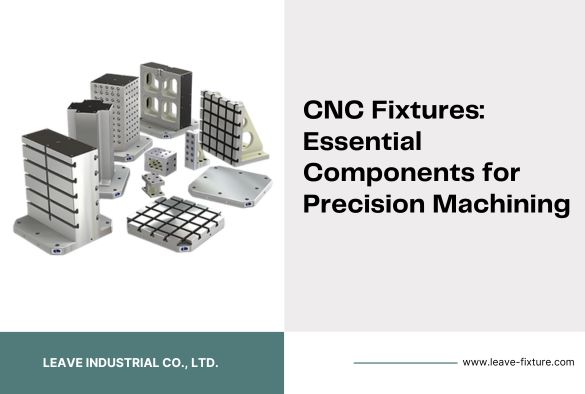
Introduction
At LEAVE, we understand the importance of precision and efficiency in modern machining. CNC fixtures are indispensable tools in this realm, providing the stability and accuracy necessary for various CNC operations. A well-designed CNC fixture securely holds workpieces in place, minimizing movement and ensuring consistent positioning throughout the machining process. In this article, we explore the purpose, types, benefits, and key considerations for using CNC fixtures in advanced manufacturing setups.
What is a CNC Fixture?
A CNC fixture is a specialized tool that secures and supports a workpiece during machining. By creating a stable environment, CNC fixtures ensure that the workpiece remains immobile, allowing for accurate cuts, drills, and other machining processes. Unlike general-purpose clamps, CNC fixtures are custom-designed or configured to hold specific types of workpieces, often incorporating precise positioning and alignment features.
Types of CNC Fixtures
There are various types of CNC fixtures, each serving specific purposes in machining:
- Modular Fixtures: These fixtures use interchangeable components, allowing machinists to reconfigure setups based on the specific shape and size of the workpiece. Modular fixtures offer great versatility and are ideal for low to medium production runs.
- Dedicated Fixtures: Custom-designed for a specific workpiece, dedicated fixtures are used in high-volume production where precision and consistency are paramount. Although they lack flexibility, dedicated fixtures excel in speed and accuracy.
- Tombstone Fixtures: Often used in horizontal machining centers, tombstone fixtures hold multiple workpieces on different faces, allowing for multi-sided machining without repositioning. This setup is efficient for high-production environments where multiple parts need machining simultaneously.
- Vacuum Fixtures: Common in industries working with delicate or thin materials, vacuum fixtures use suction to hold the workpiece in place without clamps, minimizing potential damage.
- Indexing Fixtures: These fixtures allow the workpiece to rotate during machining, facilitating operations on multiple faces of the workpiece without requiring manual repositioning.
Benefits of CNC Fixtures
Using CNC fixtures in machining offers numerous advantages:
- Improved Accuracy: By securely holding the workpiece in place, CNC fixtures reduce unwanted movement, ensuring consistent accuracy throughout the machining process.
- Enhanced Efficiency: CNC fixtures streamline setup and alignment, reducing the need for frequent adjustments. This leads to faster cycle times and increased productivity.
- Greater Flexibility: Fixtures like modular and indexing fixtures allow for reconfiguration and rotation, making them suitable for a variety of tasks and reducing the need for multiple setups.
- Cost Savings: CNC fixtures reduce the risk of workpiece damage by maintaining stability, leading to fewer reworks and material waste, which lowers production costs.
Applications of CNC Fixtures
CNC fixtures are used across multiple industries for tasks requiring precision and repeatability:
- Automotive Manufacturing: CNC fixtures help produce intricate automotive components with high consistency and accuracy.
- Aerospace Components: Aerospace parts require strict tolerances, and CNC fixtures ensure precise positioning for optimal machining quality.
- Medical Equipment: The medical industry demands high accuracy in equipment production, where CNC fixtures help in achieving exact dimensions and smooth finishes.
- Electronics: For complex electronic housings and small components, CNC fixtures provide stability for intricate machining processes.
Key Considerations When Choosing CNC Fixtures
When selecting a CNC fixture, several factors should be considered:
- Workpiece Material and Shape: The fixture should be compatible with the material and shape of the workpiece to avoid damage or slipping.
- Production Volume: Choose modular fixtures for low to medium production runs, while dedicated fixtures are more suitable for high-volume production where speed and precision are required.
- Machine Compatibility: Ensure that the fixture is compatible with the CNC machine, particularly in terms of size, mounting, and weight capacity.
- Cost and Longevity: Consider the durability and long-term return on investment. Investing in high-quality fixtures reduces maintenance and replacement costs over time.
Explore LEAVE's CNC Fixtures
At LEAVE, we offer a range of high-precision CNC fixtures designed to enhance machining efficiency and accuracy. Our fixtures include modular setups, tombstone configurations, and dedicated solutions tailored to meet the needs of various industries. With a focus on quality and durability, LEAVE's CNC fixtures help streamline operations and ensure reliable, repeatable results in every project.
Conclusion
CNC fixtures are fundamental tools in modern machining, providing stability, precision, and efficiency across multiple applications. By carefully selecting the right fixture for each operation, manufacturers can optimize productivity, reduce errors, and improve overall production quality. To learn more about LEAVE's CNC fixture solutions and how they can benefit your machining needs, contact our expert team today.